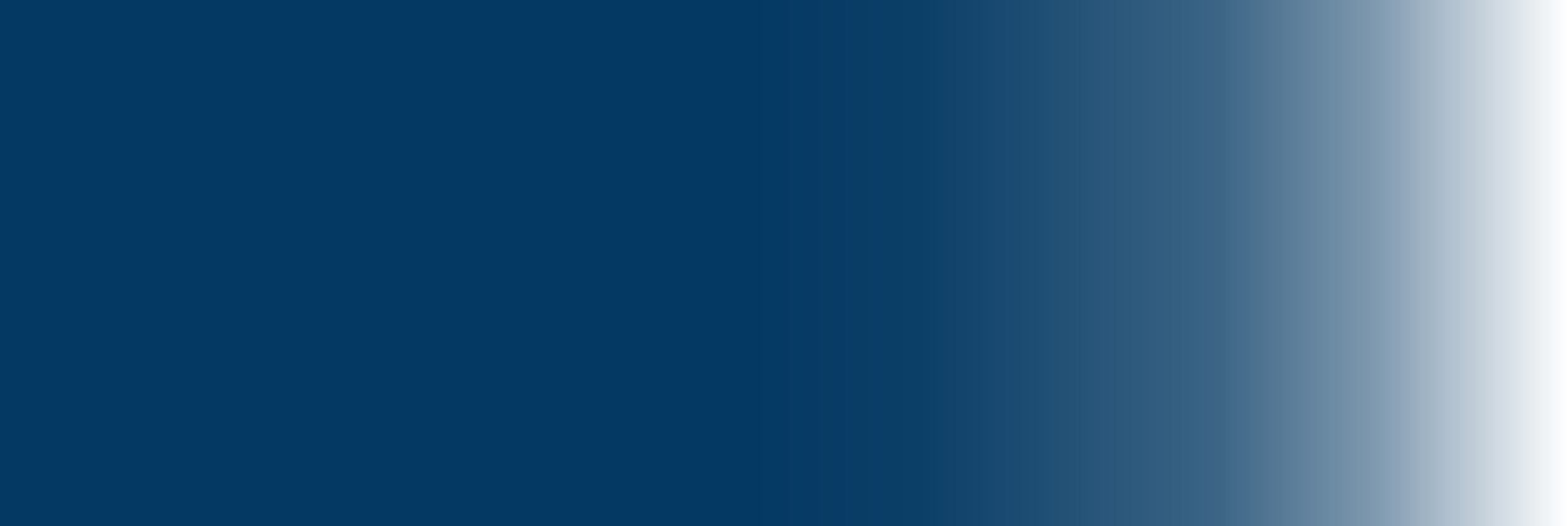
What is the Trac Skirt?
The TSI Trac Skirt System (TSS) is an award-winning and innovative conveyor skirt system that is fully adjustable, removable and safe.
Save time and money while increasing safety and minimising dust with TSI’s new, fully adjustable and removeable conveyor skirt system, the Trac Skirt System.
Advantages
This innovative system improves on vital elements of skirt refit and repair and will bring about real cost and time savings to all customers through:
a substantial reduction in the amount of time required to replace boards and skirt liners
a high degree in the accuracy of adjustment on the skirt wear plates
elimination of the need for any confined space entry
no longer having to manually‐handle the skirts
the ability to now use longer and heavier wear plates
existing dust sealing and wear liner arrangements can be retained if requested
TSS has its own innovative seal arrangement which will minimise the cost of expensive skirting
History
Trac Skirt International (TSI) has purchased all rights to the Trac Skirt System.
TSI understands and identified the innovation that the Trac Skirt has provided to clients where the system was previously installed. TSI is looking to expand the system in Australia whilst looking for opportunities to expand into overseas markets.
The TRAC SKIRT SYSTEM™ is a fully adjustable, removable and a safer conveyor skirt system, which enables a changeout in minutes compared to hours (six minutes in the controlled video demonstration).
With safety as our priority, the Trac Skirt System ensures manual handling is significantly reduced, meaning:
At NO time, does the maintainer place any part of their body into the inner skirt area or near the belt, eliminating the need to work in a confined space
Longer liners can be used and adjusted in a fraction of the time, reducing the number of gaps between liners and minimising spillage.
Liners can be locked in both directions using lock washers
Site dust sealing options can be easily retrofitted to the TSS
Inner liner plates can be quickly and positively adjusted using the offset washer
Wear on the plates can be checked externally without getting into the chute or having to stop the belt
Sealing arrangement effectively manages both dust and egress of material
More on Features
By the operation of an OFFSET WASHER at either end of each plate, maintenance workers can adjust the skirt to the desired height quickly and effectively. Once the outside OFFSET WASHERS have been adjusted on an individual plate to the correct height any remaining fasteners for the wear liner can be tensioned.
Typically, in shutdown maintenance, the skirt system is one of the last activities undertaken before deisolating. Skirt maintenance is normally reliant upon chute and belt activities finishing before skirts may be repaired or adjusted. These are usually considered critical path. Repairs and maintenance to Skirts often cannot be started until these are completed.
With the TRAC SKIRT SYSTEM™, removal and installation can be undertaken safely whilst working in with both crews. In doing so, any final adjustments once belts may be tensioned can be undertaken extremely quickly if warranted. This enables the Skirt work to be carried out jointly and not simply cancelled at the end due to others having over runs.
Our system minimises risk and provides greater efficiencies for your conveyor maintenance.
Our trolley guide rail allows for easy removal and refit of the skirt and is easily retrofit to the current structure along any length of the conveyor.
Two trolleys are required for each skirt panel (left and right sides). Using this method, a 2.4m skirt panel is easily removed without the need for confined space entry or excessive manual handling. The time taken to perform this activity is around six minutes. This is a notable improvement on the hours typically required to undertake this task. Skirt sizes can be customised to suit.
Adjustment of the internal skirt liner is made from outside the chute, which means a safer technique. If the entire panel is removed then this can be achieved in far less time, and again, without manual handling or the need for confined space.
The above mentioned is demonstrated in the video below. Here you will be able to see the ease and speed in which a panel can be removed, complete with wear liner.
Our system brings about considerable advantages for global miners.
We guarantee the TRAC SKIRT SYSTEM™ will enable each conveyor shut or planned maintenance activity to be faster, more productive and offers a step‐change to safety, risk and total cost of ownership.
TSI International has reported more than 50% improvement in the time required to perform maintenance using the TRAC SKIRT SYSTEM™.
The TRAC SKIRT SYSTEM™ can be fitted into existing infrastructure with minor to no changes required.
The TRAC SKIRT SYSTEM™ can be fitted into existing infrastructure with minor to no changes required.
The TRAC SKIRT SYSTEM™ is revolutionising the way CUSTOMERS maintenance teams undertake skirt maintenance for the future and will deliver better outcomes for your conveyors in:
safety
productivity
total cost of ownership
planning
Benefits
-
Our system provides the ability to perform a visual inspection of the skirt area quickly and efficiently, without the need to enter the chute.
-
Can be performed in minutes as opposed to the current work allocation of hours.
-
Faster changeouts means labour cost savings, with maintenance and service costs reduced.
-
Workers are not required to perform any manual lifting in the skirt area.
-
At no time does a worker place any part of their body into the inner skirt area, eliminating the need for confined space permits and making the skirt adjustment and changeout activity a safer one for workers.
-
Longer liners can be installed and adjusted in a fraction of the time, reducing the number of gaps between liners. By using longer liners, height discrepancies between liners are removed, eliminating catch points in the material flow, which causes conveyor skirt wear.
-
Liner plates can have their remaining adjustment known through a visual inspection and through the adjustment of the OFFSET WASHER, the liner can be quickly and accurately be set to the standard.
-
Enable adjustments to be extremely fine to get clearances of 1mm or less if required.
-
Makes it possible to see, from the outside of the chute, when a skirt has been rotated.
-
By virtue of our skirts being able to be adjusted, to the belt and minimising the distance between belt and liner the end result means less dust and spillage. Combined with the TSI unique sealing arrangement, dust mitigation is significantly reduced.
-
The time taken to changeout our TRAC SKIRT SYSTEM™ is a known quantity; therefore maintenance planners can take advantage of opportune maintenance and be confident in planning activities being executed on time.
-
The TRAC SKIRT SYSTEM™ presents a significant reduction in skirt wear. Liner adjustments can be made to within 1mm (if required). Our patented OFF SET WASHERS can be custom designed to obtain your optimal level of adjustment.
-
Our patented OFF SET WASHERS can be custom designed to obtain increments of adjustment to suit. We minimise overall boil point between the belt and skirt.
-
Our additional sealing system is easily retrofitted to the TRAC SKIRT SYSTEM™ preventing fugitive dust. With our sealing arrangement, we have demonstrated the ability to reduce dust emissions significantly.
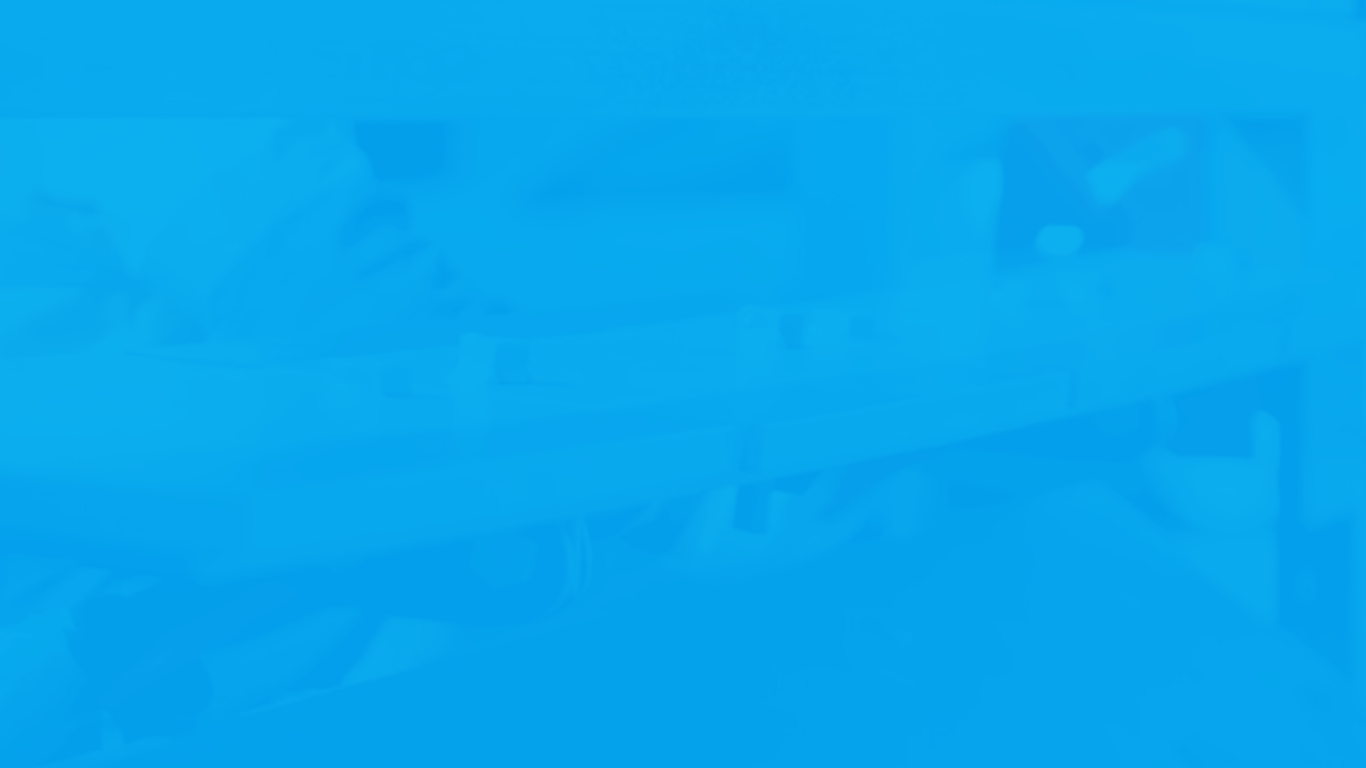
Connect with Trac Skirt International
Find out how to extend the life of your conveyor in the skirting area.